Additive manufacturing is a broad term encompassing a huge range of processes and materials; each one has its own niche and purpose. Arguably, the two most common forms of metal additive manufacturing are Laser Powder Bed Fusion (LPBF) and Wire Arc Additive Manufacturing (WAAM).
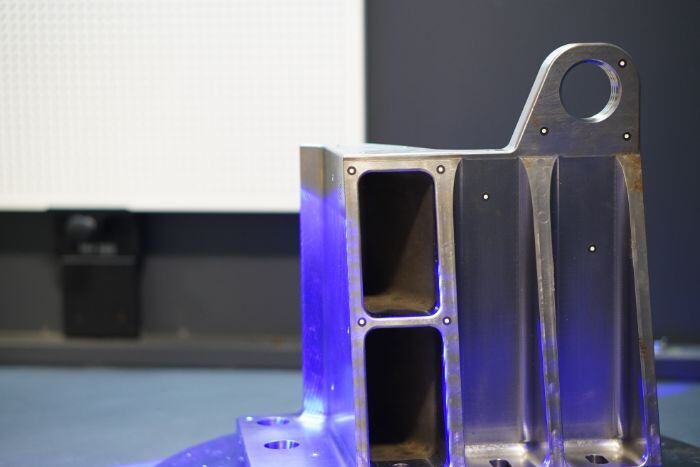
A finished product created through WAAM.
Between them, the two technologies provide different benefits and should be targeted at different applications. In this article, we’re going to break down the reasons for choosing these manufacturing processes, what the common applications are, and provide examples of the technology in action.
Laser Powder Bed Fusion
LPBF is a powerful technology that is growing in terms of usage and applications. Generally speaking, for an LPBF application to be suitable, the part you are planning to produce should have a performance benefit over an equivalent part produced via conventional methods.
This is because LPBF is relatively expensive, both in terms of machines and materials, and is generally quite a slow process. If you’re planning to produce a high number of uncomplicated parts, a more conventional machining process is almost certainly going to be a better option. With that in mind, here are the most common applications for LPBF:
Medical
Within the medical industry, there is a strong demand for high-value, customised parts, especially in regards to hip implants and maxillofacial implants. This application takes excellent advantage of the performance benefits associated with LPBF, such as the ability to create surface porosity or structures for tissue anchoring.
Each human body is unique, so many implants need to be bespoke to fit; LPBF can produce custom, high-performance parts quickly without changing tooling. A 3D scanned facial implant, for instance, can go from data to finished part in a relatively short amount of time through LPBF.
Example
Orthopedic device manufacturer, Stryker, has employed LPBF to produce complex orthopaedic implants. According to Stryker, LPBF enabled “new geometries that we couldn’t otherwise make”, as well as rapid concept development and prototype iteration.
Aerospace/Space
The complex systems that keep planes airborne often rely on high-performance parts; manufacturers often choose to adopt LPBF to make these parts, especially heat exchangers, combustors and other jet engine components.
In recent years, aerospace manufacturers have utilised LPBF to consolidate the manufacturing process of their parts. While previously, a part may have been constructed from an amalgamation of smaller components, LPBF is capable of producing a solid component, creating opportunities for increased performance and weight reduction.
Much like the journey of the automotive industry over the last two decades, the aerospace industry is currently working towards significant reductions in carbon emissions. LPBF can create more efficient aircraft manufacturing processes and componentry, helping the aerospace industry move closer toward net-zero.
Example
UK aerospace company Orbex recently designed the world’s largest metal rocket engine 3D printed in one piece. The rocket engine was optimised for selective laser melting; compared to other launch vehicles, weight is down by 30% and efficiency up by 20%.
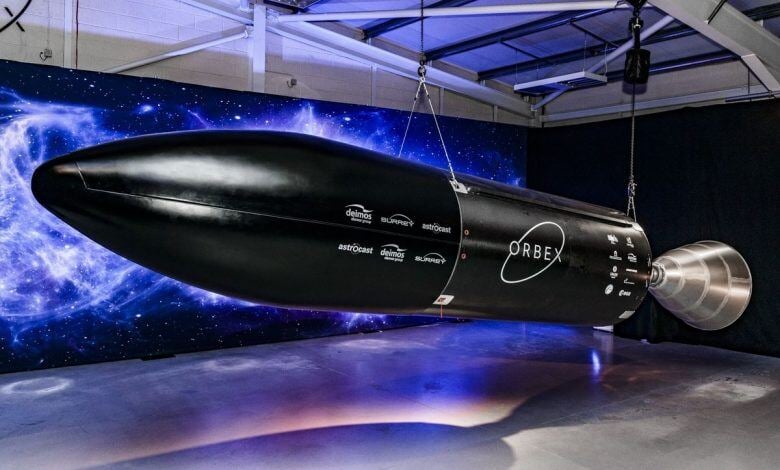
Rocket engine produced with LPBF.
Motorsport
In the motorsport industry, manufacturers use LPBF to produce high-performance parts for engines, chassis, suspension, exhaust systems and accessories for a wide variety of cars, including Formula One, hill climb and rallycross. These manufacturers take traditionally manufactured parts and redesign them for AM to reduce their weight and optimise dynamic properties.
LPBF is great for smaller batch sizes or prototyping, where part performance is paramount; this makes LPBF a fantastic application in the motorsport industry. Recently, multiple Formula One engine manufacturers have used LPBF to create a wide range of componentry where temperature resistance and strength are critical:
- Roll hoops
- Cooling plates
- Hydraulic blocks
- Pump housings
- Cooling pipes
- Wing structures
- Turbine and compressor castings
Example
Race engine designer PIPO Moteurs used LPBF to manufacture an exhaust assembly for their Rallycross and Rally inline-four engine. This exhaust assembly consisted of 6 additively produced parts, yielding an 18.9% mass saving and reduced welding failure risk.
Tooling
Tooling is arguably the most common application for LPBF, particularly when manufacturing mold and dies. LPBF is unrivalled when metal parts need to contain complex geometries or channels; manufacturers can create parts with significant performance improvements in terms of conformal cooling.
Example
Mold and die manufacturer iQtemp have a number of case studies outlining the performance advantages LPBF affords their products. For instance, a sophisticated cooling core designed for one client reduced cycle times from 70 seconds to 42 seconds.
Summary: Laser Powder Bed Fusion
For LPBF to be a suitable application, part performance should be a priority, rather than cost or speed of production. What’s more, significant investment is needed in the design phase to ensure LPBF is the best manufacturing technology. If LPBF isn’t in the front of a designer’s mind from the very beginning, it’s unlikely to be the correct choice of tool.
Wire Arc Additive Manufacturing
WAAM is very different technology from LPBF, further emphasising the range of processes under the additive manufacturing umbrella. Unlike LPBF, WAAM creates parts with far less resolution but with much higher deposition rates. This means that parts made with WAAM are less precise, but they’re produced faster; consequently, some part performance benefits are removed for production speed.
There aren’t specific industries that are known for employing WAAM. Instead, good applications for WAAM are where the customer needs to reduce inventory or find lower lead times through condensed development cycles and forging time. For instance, in the rail industry, manufacturers employ WAAM to produce high-value, low-volume parts quickly and efficiently. There’s a convenience factor associated with WAAM; it’s fast and easier to comprehend than LPBF.
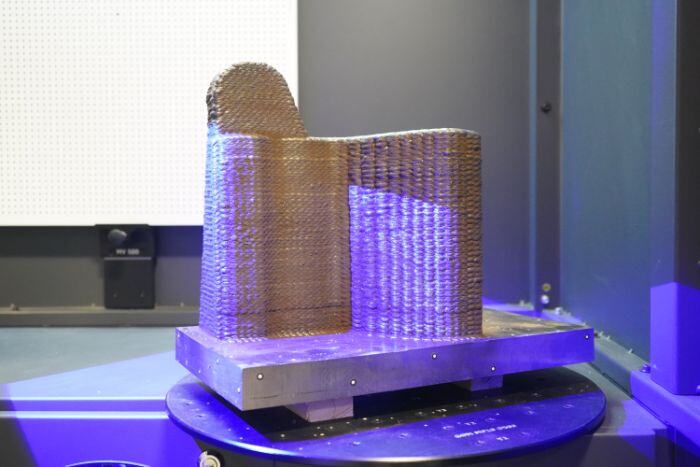
A component for Deutsche Bahn part way through production.
Example
These examples from GEFERTEC highlight the fast and flexible procurement WAAM provides to various industries, from marine diesel engine parts to hot forming dies. The examples highlight reduced delivery times and costs, as well as material savings of up to 80%.
So, what can we learn?
The applications for additive manufacturing are varied and diverse. Additure has adopted LPBF for its manufacturing potential, and WAAM for its speed and ease of comprehension.
For Additure, ‘What are the applications of additive manufacturing?’ isn’t the correct question to ask; instead, we should ask ourselves, ‘Is this type of additive manufacturing suitable for this component/product?’.
Who are Additure?
We’re on a mission to simplify additive manufacturing – if you have questions about the technologies discussed here, your processes, or the feasibility of a product, speak to the Additure team today.